He is a fellow of the Royal Society of Canada, a member of the Canadian Academy of Engineering, a recipient of Canada's highest national science and technology award, and the Chief Scientist of Canada. At the age of 44, he became the youngest fellow of both academies in Canada.
Previously, he served as the director of the Advanced Materials for Clean Energy Laboratory at the University of Waterloo in Canada and the director of the Electrochemical Energy Center at the University of Waterloo. His name is Zhongwei Chen.
In 2023, Zhongwei Chen returned to China full-time to join the Dalian Institute of Physical Chemistry. Not long ago, he and his domestic team designed a one-step battery recycling process.
This is a high-value recycling method that, by choosing more environmentally friendly organic acids, not only greatly improves the efficiency of battery recycling but also reduces the cost of battery recycling.
At present, more than 90% of China's nickel and cobalt resources rely on imports, and waste lithium batteries contain these high-value metal elements.In 2022, China recycled a total of 300,258 tons of waste lithium batteries. Among them, there were 188,692 tons of ternary waste materials, 94,551 tons of lithium iron phosphate waste materials, and 17,015 tons of lithium cobaltate waste materials.
Advertisement
The high value-added recycling method proposed by the research group, with the help of a one-step method, can leach and recover high-value metal elements from the retired and recycled cathode materials, and then use them as raw materials to carry out a co-precipitation process through a one-step method, thereby regenerating them into brand new cathode materials.
Subsequently, the cathode materials can be used in the next generation of low-cost, high-safety sodium-ion batteries, achieving a transition to the next generation of energy storage batteries.
Nowadays, the price of lithium carbonate has risen to more than 450,000 yuan per ton. Under this situation, the advantages of sodium-ion batteries are becoming more prominent. The price of sodium chloride, which uses sodium as the raw material, is only a few thousand yuan per ton, while its safety and low-temperature performance are also higher.
In this study, the team transformed the retired lithium-ion battery cathode materials into low-cost sodium-ion battery cathode materials through recycling methods, greatly reducing the cost of energy storage batteries and paving the way for the commercialization of low-cost sodium-ion batteries.Recently, the relevant paper was published in Nature Sustainability (IF 27.6) under the title "Sustainable regeneration of spent cathodes for lithium-ion and post-lithium-ion batteries."
Yang Tingzhou is the first author, and Academician Chen Zhongwei and Researcher Zhang Yongguang from the Dalian Institute of Chemical Physics are the co-corresponding authors.
Laying out the blue ocean market in advance
In fact, the research team carried out this study based on a grand new energy background. In 2023, a total of 14.2 million new pure electric vehicles and plug-in hybrid vehicles were delivered worldwide.Electric vehicle sales in the United States and Canada have grown by 46% year-on-year, while in China, they have increased by 36% year-on-year.
In stark contrast to the booming production and sales of electric vehicles is the low standardized recycling rate of retired power batteries, which cannot meet the upcoming large-scale centralized retirement of new energy vehicles, thus the recycling dilemma of power batteries urgently needs to be resolved.
The recycling of power batteries mainly includes cascade utilization and recycling utilization.
In cascade utilization, if the battery capacity is between 20%-80%, it can be used for energy storage power stations, two-wheeled electric vehicles, solar energy storage systems, communication base stations, etc.
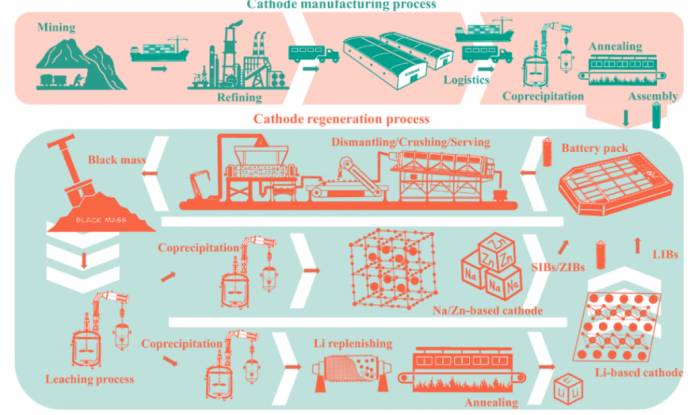
In recycling utilization, if the battery capacity is below 20%, it needs to be scrapped and dismantled, and then extract the high-value metal elements inside.At present, commercial recycling mainly adopts a complex three-step process of extraction, precipitation, and calcination, and uses strong acids as extractants, which makes it difficult to recycle and treat the waste liquid.
For many years, the team has taken the demand for new types of battery technology with low cost, high capacity, high safety, and high convenience as the starting point, focusing on issues in the field of power batteries, and carried out interdisciplinary research integrating electrochemistry, energy, materials, artificial intelligence, and other disciplines.
The research group learned that: only in 2023, the total amount of retired power batteries in China exceeded 580,000 tons. It is expected that by 2030, the scale of China's power battery recycling market will break through 100 billion yuan.
Such a huge market scale has prompted them to carry out continuous research on the sustainable recycling of power batteries, thereby laying out this blue ocean market in advance.
In recent decades, with the advancement of technology and the reduction of costs, lithium-ion batteries currently dominate in industries such as consumer electronics and transportation electrification.However, both of the aforementioned driving factors are showing signs of slowing down.
In the field of lithium-free technology, sodium-ion batteries are considered to be one of the most promising technologies.
According to data released by CATL (Contemporary Amperex Technology Co., Limited), the company's first-generation sodium-ion batteries have an energy density of 60Wh/kg, which can store more than 80% of the electricity after charging for 15 minutes at room temperature, and have a discharge retention rate of over 90% in low-temperature environments of minus 20 degrees Celsius.
---
Achieving the transition to low-cost sodium-ion batteries.Earlier, Chen Zhongwei's team discovered in their research on sodium-ion batteries and the next generation of high-performance sodium-based cathode materials that the transition metal elements required for sodium-based cathodes coincide with the high-value transition metal elements rich in retired power batteries.
Thus, they envisioned designing a recycling plan to achieve a transformation to low-cost sodium-ion batteries through battery recycling.
At the beginning, the research group set the "four highs" research goals: high efficiency, high safety, low cost, and high performance.
After gaining a deep understanding of the battery recycling process, they modified the fully mixed anaerobic reactor used in the preparation of lithium battery cathodes before, and then created a one-step cathode regeneration process.
Based on the doping process designed by the team for sodium-based cathodes in the early stage, after nearly a hundred adjustments to the formula, they finally prepared a variety of sodium-based cathode materials using retired cathode materials.The structure of these materials exhibits a uniform cubic shape, and all possess high performance.
To further verify the feasibility of sodium-based cathode materials, the research team conducted pilot scale-up experiments and intermediate scale-up experiments. The experimental results show that these sodium-based cathode materials can meet the requirements for commercial scale-up.
In order to compare the one-step battery recycling process with the traditional three-step recycling process, the team established a complete set of life cycle analysis models and economic technical analysis models.
Through this, the research team conducted simulation analysis for the full life cycle of power battery technology and battery recycling technology, from raw material metallurgy to the end-of-life battery recycling, and discussed the feasibility and profit margins of related battery technologies.
According to the introduction:The full life cycle analysis involves all aspects from the extraction of raw materials, production, use, to disposal.
This includes the impact of raw material extraction on the environment, energy consumption and emissions during the production process, the use phase of the battery, and the disposal methods of discarded batteries.
The economic and technical analysis involves an assessment of the production cost, efficiency, sustainability, and market prospects of lithium batteries.
Factors such as input and output during the production process, as well as the performance, lifespan, and cost-effectiveness of the battery will be considered.
By comprehensively considering both the full life cycle analysis and the economic and technical analysis, it is possible to better evaluate the feasibility and sustainability of lithium batteries as an energy storage solution, as well as their role and development trend in the energy system.It is understood that recycling and reusing power batteries not only reduces the cost of manufacturing new batteries but also significantly reduces carbon emissions throughout the battery's life cycle, thereby promoting green and low-carbon development.
In the future, the team will continue to focus on the sustainable recycling of retired power batteries, working from three aspects: battery design, battery crushing separation, and cathode material regeneration.
In terms of battery design, it is necessary to consider the convenience of recycling and disassembly during the design phase.
In response to this:
Firstly, modular design can be adopted to make battery components easier to separate and replace.Secondly, the use of environmentally friendly and renewable materials can reduce the use of harmful substances, helping to lower environmental pollution during the recycling process.
Again, by marking the types and proportions of battery materials, it facilitates classification and treatment during the recycling process.
Lastly, the development of reusable battery packaging and casings can also improve overall recycling efficiency.
For the crushing and separation of retired power batteries, the research team plans to first mechanically crush the batteries into smaller particles, and then use physical and chemical methods for separation. For example, magnetic suspension technology and flotation technology can effectively remove impurities and improve the purity of the cathode materials.
In terms of the sustainable regeneration of cathode materials, the team will further screen different environmental protection extraction solutions and cathode preparation methods for use in the regeneration process of cathode materials, contributing to the improvement of the quality and efficiency of regenerated materials.The combination of these measures is expected to not only enhance recycling efficiency but also promote the sustainable development of the battery recycling industry.
Integrating artificial intelligence technology, the first generation of the battery digital brain, PBSRD Digit 1.0, has been launched.
At the same time, the research team has also been focusing on the application of artificial intelligence in the field of materials.
Recently, they introduced the first generation of the battery digital brain, PBSRD Digit 1.0. This system, by combining electrochemical models and artificial intelligence technology, is capable of early warning of battery faults, state estimation, and life prediction functions.According to the introduction, the core of the first-generation battery digital brain lies in building a model framework of "electrochemical model + artificial intelligence."
This model framework not only improves the accuracy of the battery management system and ensures the safety and reliability of the battery, but also continuously optimizes its own performance and achieves self-improvement through machine learning.
By leveraging the team's accumulation in the field of electrochemistry and combining the data processing and pattern recognition capabilities of artificial intelligence, they have developed an intelligent algorithm that can monitor the battery status in real-time, predict the battery health status and remaining service life.
In addition, they have also established a cloud database of battery performance, collecting and analyzing battery data from different scenarios and working conditions, and using these data to train and verify algorithm models to ensure the high reliability and adaptability of the battery digital brain.
It is also reported that Academician Chen Zhongwei joined the Dalian Institute of Physical Chemistry in 2023, and then established the Academic Committee of the National Key Laboratory of Energy Catalysis Transformation and the Department of Power Battery and System Research.Currently, Zhongwei Chen has assembled a research team and an engineering team consisting of over a hundred members.
Among them:
The research team generates new scientific and technological achievements through experiments and research; the engineering team is responsible for transforming these achievements into feasible products or solutions.
Through this, Zhongwei Chen hopes to accelerate the commercialization process of scientific research results, achieving a seamless connection from scientific discovery to market implementation.